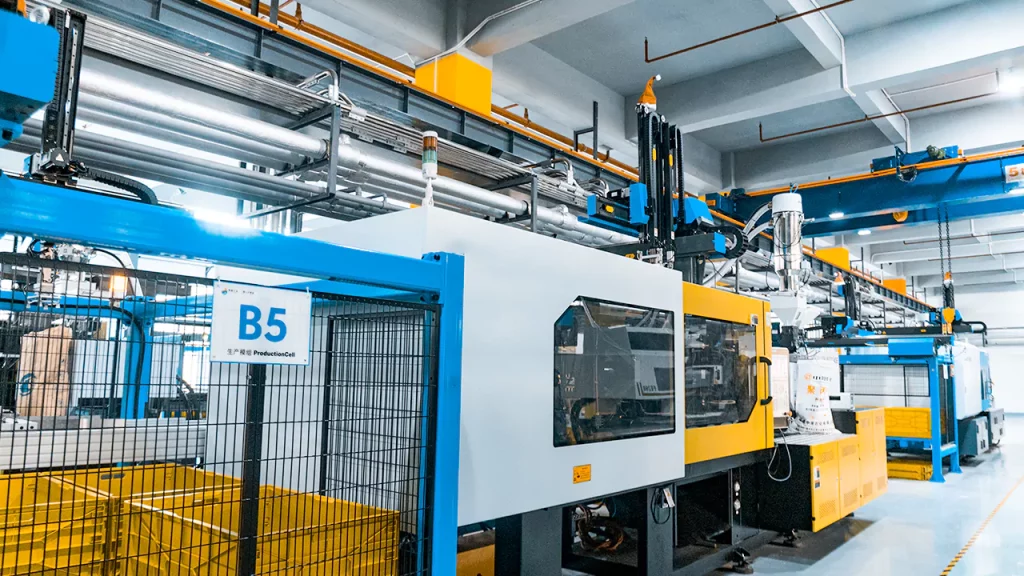
How Prototype Molds Are Revolutionizing the Manufacturing Industry
Key Takeaways
- Prototype molds are essential in speeding up product development cycles.
- The use of prototype molds reduces overall production costs.
- Technological advancements in prototype molds have significantly impacted various industries.
What Are Prototype Molds?
Prototype molds are custom-molded tools used to create initial samples of a product. These samples, often called prototypes, are evaluated for design, fit, and function before full-scale production begins. The importance of prototype molds in the manufacturing process cannot be overstated. They are critical for identifying potential design flaws and functional issues early in the product development cycle, thereby minimizing costly errors. This is especially relevant in injection molding, where the precision of molds can significantly influence the quality and functionality of the final product.
Benefits of Using Prototype Molds
Using prototype molds presents several noteworthy benefits that can make a substantial difference in manufacturing. Firstly, they facilitate rapid prototyping, allowing for faster design validation. This speed is critical in competitive industries, where time-to-market can define success or failure. Secondly, they lead to significant cost savings regarding materials and labor. By identifying and addressing issues early on, businesses can avoid wasting resources on defective products. Moreover, prototype molds improve product quality and reliability, ensuring the final products meet or exceed consumer expectations.
Technological Advancements in Prototype Molds
The rapid pace of technological advancements has significantly shaped the landscape of prototype molds. Notably, 3D printing and Computer-Aided Design (CAD) have drastically enhanced the capabilities of prototype molds. These technologies allow for the creation of more complex and precise designs. With 3D printing, manufacturers can quickly produce detailed prototype molds that mimic the final product’s material properties and structural integrity. CAD facilitates intricate design alterations without the need for physical modifications. These advancements have made testing and refining products easier before they enter mass production, leading to better final products and reduced timeframes.
Cost Efficiency and Speed
One of the most compelling advantages of using prototype molds is their ability to reduce both the time and cost associated with product development. Prototype molds shorten the product development cycle by allowing for early design and detection of functional issues. This is especially important in industries with high competition, as being first to market can give you a significant competitive advantage. Companies that leverage prototype molds have reported a 30% to 50% reduction in product development times. Due to this reduction, businesses can invest in more innovation and allocate their resources more effectively, which results in significant cost savings.
The Future of Prototype Molds
The future of prototype molds looks promising, driven by continuous advancements in materials science and digital manufacturing technologies. As these fields evolve, the capabilities of prototype molds will expand, offering even greater flexibility and faster turnaround times. Innovations such as advanced composite materials and more sophisticated 3D printing technologies are expected to further enhance the precision and durability of prototype molds. This will enable businesses to push the boundaries of innovation, creating complex products with unprecedented efficiency. The ongoing development in this area will likely make it easier for businesses of all sizes to bring their ideas to life, fostering a more dynamic and competitive market landscape.